Alüminyum Kaynağı Nasıl Yapılır? Alaşım Elementlerinin Alüminyum Üzerindeki Etkisi Nedir?
Alüminyum kaynağının daha zor olduğuna dair genel bir düşünce vardır. Bu daha çok kaynak reçetesine uyup uymamanızla ilgilidir. Doğru yöntem ve ekipmanları bir araya getirerek gerek gaz altı alüminyum kaynağı, gerek argon alüminyum kaynağının o kadar zor olmadığını göreceksiniz.
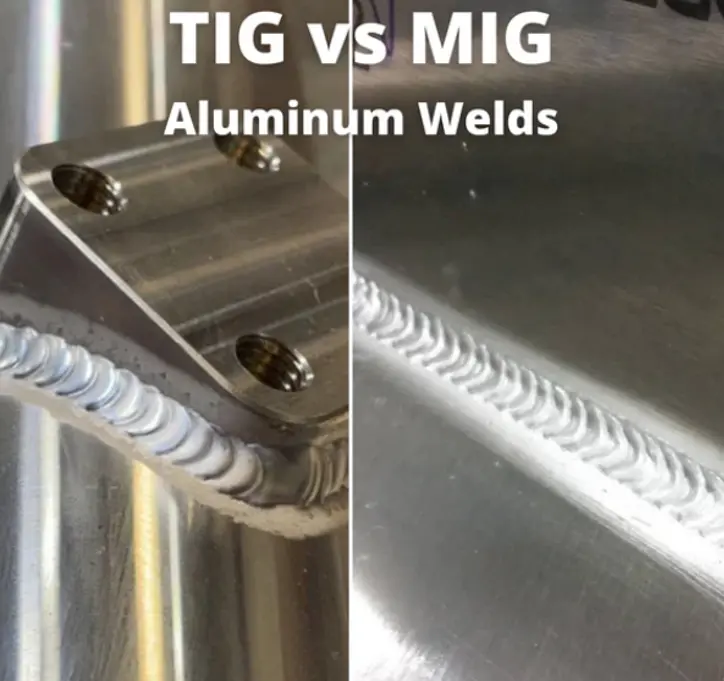
Doğru bir reçete oluşturmanın ilk adımı kaynatacağımız malzemeyi tanımaktan geçer. Alüminyum alaşımlarının kimyasal kompozisyonu ve buna bağlı olarak kaynakta vereceği reaksiyonları önceden bilmek işimizi çok kolaylaştıracaktır.
Alüminyum alaşımları
Saf alüminyum oldukça yumuşak ve mekanik özellikleri aşağıda bir metaldir. Bu yapısı kaynaklanabilirliğini ve kaynak sonrası servis koşullarını kötü yönde etkiler. Alaşım elementleri ile birleştiğinde çeşitli mekanik özellikleri açısından zengin bir hal alır. Bu alaşımlar dört basamaklı tanımlama sistemi ile ana alaşımları baz alarak sınıflandırılır. Her bir alaşımın etkisi aşağıda yer verilmiştir.
BAKIR (Cu)
Alüminyuma katkı olarak ilave edilen temel alaşım elementlerindendir. % 1-12 oranları aralığında katılırlar. Alaşımdaki Cu (bakır) miktarı arttıkça alaşımın akıcılığı, çekme dayanımını(gerilmesi) ve sertliğini artar. Cu(bakır) iç büzülmeleri azaltır, alaşımın işlenebilme kabiliyetini artıran alaşım elementidir. Aynı zamanda sıcak yırtılmaya karşı mukavemeti azalttığından dökümü zorlaştırır. Dövme alaşımlarda Cu(bakır) %3-5 oranlarında kullanılmaktadır. Cu(bakır) oranı %5‟ten fazla kullanıldığı zaman malzemenin mekanik olarak işlenebilmesi güçleşir. Ayrıca korozyon direncini azaltır ve elektrik iletkenliğini düşürür. Döküm alaşımlarda ise %12 ye kadar kullanılabilirse de, genellikle %10‟dan fazlası kullanılması tercih edilmemelidir
SİLİSYUM (Si)
Alüminyuma %20’ye kadar ilave edilebilir(hiper ötektiküstü). Si(silisyumun)’la beraber bir miktar Mg katılarak ısıl işlem uygulanabilen döküm parçalara Al-Si alaşımları meydana getirirler. Bu alaşımların çekme mukavemetleri yüksek olmayıp 13.6-15.4 Kg/mm² arasında değişir. Korozyon dirençleri, ısıl ve elektrik iletkenlikleri yüksek, genleşmeleri düşüktür. Bu alaşımların korozyon direnci yüksek fakat işlenebilmesi zordur(Silisyum miktarı arttıkça işleme kabiliyeti zayıflar). Döküm alaşımlarda %12’ye(ötektik yapı) kadar Si alaşımın akıcılığını ve yüksek sıcaklık dayanımını artırır.
MAGNEZYUM (Mg)
Mg(Magnezyum) ilavesi bir cüruflaşma meydana getirdiği için alüminyum alaşımlarının dökümünü zorlaştırır. Bunu önlemek için malzemeye Be (berilyum) ilave edilir. Özel parça dökümlerde tekrar ergitme esnasında dikkat edilmelidir.Zira malzeme oksitlenme ve Mg kaybetme eğilimindedir. Oluşan oksitleri gidermek için sisteme klor gazı verilir(sağlık ve çevre açısından olumsuzlar meydana getirir. %8 Mg içeren alüminyum alaşımlarının korozyon dirençleri yüksek ve anodik oksidasyon (eloksal kaplama) özellikleri iyidir.
MANGAN (Mn)
Mn (Mangan) tane küçültücü bir rol oynar. Alaşımın korozyon direncini azaltmadan çekme mukavemetini artırır. Bakır ve silisyum alaşımlarına ilave edildiği zaman yüksek sıcaklıkta dökülen dökümün mukavemetini artırır. Manganın demirle reaksiyona girmesine (birleşmesine) izin verilmemelidir. Aksi takdirde oluşan büyük tanecikler alaşımın mukavemetini düşürür. Manganın ısıl işleme bir etkisi yoktur. Al-Mn alaşımlarına ısıl işlem uygulanamaz. Mangan alaşımın ergime noktasını yükseltir.
ÇİNKO (Zn)
Zn(Çinko) bazı alüminyum alaşımlarında istenmeyen yabancı(empürite) eleman olarak bulunur. Artan çinko miktarlarında alaşımın akıcılığı artmakla beraber yüksek sıcaklık dayanımı azalır. Soğuma esnasında büyük çekilmeler,çekmeler oluşur. Olumlu bir sonuca ulaşmak için dökümün hızlı soğutulması ve büyük çıkıcılar(şişler) kullanılması gerekir. Çinko katkısıyla bütün alüminyum alaşımlarının haddelenebilme kabiliyeti iyileşir. Özellikle magnezyumla beraber ilave edilirse haddelenme kabiliyetini artırdığı gibi yüksek çekme ve darbe mukavemeti de sağlar.
TİTANYUM (Ti)
Alüminyum alaşımlarında tane küçültücü bir etki gösterir. % 0,05-0,250 sınırları arasında ilave edilirler. Basınçlı döküm alaşımlarına Ti ilavesi zararlıdır. Çünkü Ti İlavesi akışkanlığı azaltır, bu durum ise döküm sırasında zorluk çıkartır. Basınçlı dökümlerde soğuma çabuk olduğundan küçük taneler kendiliğinden oluşur. Titanyum çekme mukavemetiyle sünekliliği artırır, ısı iletkenliğini ise azaltır. Endüstride Ti Bor (AlTiB) ile beraber kullanılır.
DEMİR (Fe)
Al-Fe alaşımları pek kullanılmazlar. Demir, alüminyum alaşımlarında empürite olarak bulunup, miktarı farklılık gösterir. Demir bazı uygulamalarda mukavemeti, yüksek sıcaklıklarda sertliği artırma gibi alaşım özelliklerini iyileştirici özelliğe sahiptir. Ayrıca sürekli döküm kalıplarının sıcak çatlamaya olan direncini artırır. Bazen de çekilmeleri azaltmak için demir ilave edilir. Demirin bir başka özelliği de tane küçültücü olmasıdır. Bununla beraber yüksek silisyumlu alaşımlarda demir miktarının fazla oluşu kaba kristalli ve gevrek bir yapıya neden olur.
NİKEL (Ni)
Nikel alüminyum alaşımlarına yüksek olmayan yüzdelerde katıldığı takdirde tıpkı bakır gibi dayanım ve sertliği artırır. Alaşıma parlaklık ve yansıtıcılık vererek yüzey kalitesini iyileştirir(parlaklık). Yüksek demir yüzdelerinin olumsuz etkilerini dengeler. Genellikle yüksek sıcaklıklarda, yüksek dayanım ve sertlik istenen alaşımlara katılır. Alaşımlardaki nikel miktarı % 0.5-3.0 arasında değişir.
KALAY (Sn)
Metal ergidikten sonra ilavesi oldukça kolaydır. Bakır ve nikelle kullanıldığı zaman çok dayanıklı bir alaşım meydana getirir. Alüminyum alaşımlarında kalay düşük ve yüksek sıcaklıklarda dayanımı düşürür. Alaşım içindeki miktarı %0,5-1.0 arasında olduğunda gevrekliği artırır ve alüminyuma göre daha katodik olduğundan korozyon direncini olumsuz yönde etkiler. Kalayın alüminyum içindeki erirliği çok düşüktür. Yatak olarak kullanılan alüminyum alaşımlarının en önemli bileşenlerinden biriside kalaydır. Basınçlı döküm alaşımlarında kalaya çok az rastlanır.
KURŞUN (Pb)
Pb(kurşun)özellikle kalay(Sn) ve bizmut(Bi) ile kullanıldığında alaşımın işlenebilme kabiliyetini artırır. %0.5 den aşağı miktarlarda ilave edilir. Alüminyuma göre daha katodik olduğundan alaşımının korozyon direncini düşürür. Alüminyum içerisindeki çözünürlüğü çok düşürür.
KROM (Cr)
Cr(Krom) genellikle % 0,10-0,60 oranlarında ilave edilir. Tane küçültücü rol oynar. Titanyumla beraber kullanılır. Al-Zn-Mg alaşımlarına, korozyon direncini artırmak ve gerilim çatlaklarını azaltmak için ilave edilir. Kromun alüminyum içindeki çözünürlüğü çok düşüktür. Burada ikinci faz çökelmesi görülmez. Bu nedenle Al-Cr alaşımlarına ısıl işlem uygulanamaz. Bünyede oluşan Cr-Al bileşikleri yüksek sıcaklıklarda mukavemeti artırıp, malzemeyi korozyona dayanıklı hale getirir. Krom da mangan gibi alaşımın ergime sıcaklığını yükseltir.
BOR (B)
Genellikle % 0.01 oranında kullanılır. Titanyumla beraber iyi bir tane küçültücüsüdür. Bor kullanılmadığı zaman titanyumun tane küçültme etkisi, tekrar ergitme esnasında azalır. Titanyum gibi bor da çekme mukavemetini ve sünekliliği artırır.
Alüminyum alaşımlarının kaynağa etkisi aşağıda ki gibidir.
1000 serisi alüminyum alaşımı
%99 oranda saflıkta olan bu serinin geri kalanını eser miktardaki elementler oluşturur. Bu serinin kullanım amacı elektrik iletkenliğini kullanmak yada yüksek korozyon direncinden yararlanmak içindir. Genellikle kullanılan kaynak telleri aşağıdaki gibidir.
DIN-EN-ISO 18273 | Si | Fe | Cu | Mn | Mg | Zn | Cr | Be | Ti | Bakiyesi | |
S AL 1050 (Al 99,5) | <0,15 | <0,15 | <0,02 | <0,02 | <0,02 | <0,04 | – | <0,0003 | <0,03 | <0,03 | |
S AL 1450 (Al 99,5 Ti) | <0,40 | <0,25 | <0,05 | <0,05 | <0,05 | <0,07 | – | <0,0003 | 0,10 – 0,20 | <0,03 |
–2000 serisi alüminyum alaşımı
Yüksek mukavemetlerinden dolayı genellikle havacılık sektöründe kullanılır. Sıcak çatlak riski en fazla olan seri olduğundan ötürü kaynaklanabilirliği en kötü olan seridir. 2319 ve 4043 alüminyum kaynak teli ile kaynayan 2219 ve 2519 gibi birkaç tane 2000 serisi alüminyum alaşımı vardır.
DIN-EN-ISO 18273 | Si | Fe | Cu | Mn | Mg | Zn | Cr | Be | Ti | Bakiyesi | |
S AL 2319 (AlCu6MnZrTi) | <0,20 | <0,30 | <6,80 | <0,40 | <0,02 | <0,10 | – | <0,0003 | <0,02 | <0,05 |
-3000 serisi alüminyum alaşımı
Mekanik özellikleri orta olan bu serinin şekillendirilmeleri oldukça kolaydır. Genellikle ısı eşanjörlerinde ve klima parçalarında kullanılır. 4043 veya 5356 ile kolayca kaynayabilirler.
DIN-EN-ISO 18273 | Si | Fe | Cu | Mn | Mg | Zn | Cr | Be | Ti | Bakiyesi | |
S AL 4043 (AlSi5) | <0,40-0,60 | <0,60 | <0,30 | <0,15 | <0,20 | <0,10 | – | <0,0003 | <0,15 | <0,15 | |
S AL 5356 (AlMg5Cr) | <0,25 | <0,40 | <0,10 | <0,05-0,20 | <4,50-5,50 | <0,10 | 0,06-0,20 | <0,0003 | <0,15 | <0,05 |
-4000 serisi alüminyum alaşımı
Birçok sektörde kullanılan bu alüminyum alaşımı mekanik değerleri kötü olmamakla birlikte kaynaklanabilirliği oldukça yüksektir. Ana malzeme olarak kullanılmasının yanı sıra 4000 serisi kaynak teli ile bir çok seriyi kaynatabildiğinden sarf malzeme olarak kullanımı da oldukça yüksektir. 4043 ile herhangi bir 4000 serisi ana malzemeyi kolaylıkla kaynatabiliriz.
DIN-EN-ISO 18273 | Si | Fe | Cu | Mn | Mg | Zn | Cr | Be | Ti | Bakiyesi |
S AL 4043 (AlSi5) | <0,40-0,60 | <0,60 | <0,30 | <0,15 | <0,20 | <0,10 | – | <0,0003 | <0,15 | <0,15 |
-5000 serisi alüminyum alaşımı
Mekanik değerleri oldukça yüksek olan bu seri bir çok sektörde kullanılsa da özellikle alüminyum yat sektöründe oldukça tercih edilir. 5087, 5183, 5356, 5754 serilerinde alüminyum kaynak telleri mevcuttur.
DIN-EN-ISO 18273 | Si | Fe | Cu | Mn | Mg | Zn | Cr | Be | Ti | Bakiyesi | |
S AL 5087 (AlMg4.5MnZr) | <0,40 | <0,25 | <0,05 | <0,70-1,10 | <4,50-5,20 | <0,25 | 0,50-0,25 | <0,0003 | <0,15 | <0,15 | |
S AL 5356 (AlMg5Cr) | <0,25 | <0,40 | <0,10 | <0,05-0,20 | <4,50-5,50 | <0,10 | 0,06-0,20 | <0,0003 | <0,06-0,20 | <0,05 | |
S AL 5183 (AlMg4.5Mn0,7) | <0,40 | <0,40 | <0,30 | <0,50-1,00 | <4,30-5,20 | <0,25 | 0,02-0,20 | <0,0003 | <0,15 | <0,15 | |
S AL 5754 (AlMg3) | <0,40 | <0,40 | <0,10 | <0,50 | <2,60-3,60 | <0,20 | 0,30 | <0,0003 | <0,15 | <0,05 |
-6000 serisi alüminyum alaşımı
Çatlama eğilimleri yüksek olduğu için kaynak reçetesine dikkat etmek gerekir. Genellikle köprülerin, kirişlerin ve bir çok yapı malzemelerinin içerisinde bulunur. İşlenebilirliği, kesilebilirliği ve kaynaklanabilirliği yüksektir. Genellikle 6061 serisi ana malzeme kullanılır. 4043 ve 5356 alüminyum kaynak teli ile kolaylıkla kaynar.
DIN-EN-ISO 18273 | Si | Fe | Cu | Mn | Mg | Zn | Cr | Be | Ti | Bakiyesi | |
S AL 4043 (AlSi5) | <0,40-0,60 | <0,60 | <0,30 | <0,15 | <0,20 | <0,10 | – | <0,0003 | <0,15 | <0,15 | |
S AL 5356 (AlMg5Cr) | <0,25 | <0,40 | <0,10 | <0,05-0,20 | <4,50-5,50 | <0,10 | 0,06-0,20 | <0,0003 | <0,15 | <0,05 |
-7000 serisi alüminyum alaşımı
Yüksek mukavemetlerinden ötürü genellikle havacılık sektöründe kullanılan bu alüminyum serisi, sıcak çatlak, yorulma ve korozyon direncinin kötü olmasından ötürü kaynaklanamazlar. 7003,7005 ve 7039 gibi istisna olan birkaç tane serisi 5356 alüminyum kaynak teli ile kaynatılmalıdır.
DIN-EN-ISO 18273 | Si | Fe | Cu | Mn | Mg | Zn | Cr | Be | Ti | Bakiyesi | ||||||
S AL 5356 (AlMg5Cr) | <0,25 | <0,40 | <0,10 | <0,05-0,20 | <4,50-5,50 | <0,10 | 0,06-0,20 | <0,0003 | <0,15 | <0,05 |
ALÜMİNYUM KAYNAĞI
Alüminyum oksit, alüminyum havaya maruz kaldığında neredeyse anında oluşur ve altındaki metalin korozyona uğramasını önler. Bu nedenle, bu yüzey tabakası alüminyumun dayanıklılığının anahtarıdır. Bu koruyucu tabaka 3700°F’de (2037°C) erirken altındaki saf alüminyum 1200°F’de (650°C) erir. Bu oksit tabakasını yırtıp aynı zamanda da alüminyuma zarar vermemek için gaz altında pulse yöntemi, argonda AC kaynak modu kullanılır.
Alüminyum Gaz Altı Kaynağı
Alüminyum gaz altı kaynağı, pulse yada double pulse kaynak modu ile yapılmalıdır. Darbeli kaynak modu (pulse) çift amperi aynı anda kullanmaya olanak tanır. Böylece üst amper oksiti kolayca yırtabilirken aynı zamanda düşük amperle de ısı girdisini minimize ederek ana malzemeye zarar vermez.
Yukarıda ki resim pulse kaynak modunun bir saniyede ki amper zaman değişimini göstermektedir. Bu şekle göre pulse frekansı 2 hz’dir. Bir saniyede kaç döngü olacağı belirlenir. Frekans alüminyum kaynağında oldukça önemli bir parametredir. Kullanacağımız kaynak makinesinin yetisi burada oldukça önemlidir. Bazı kaynak makinelerinin frekans aralığı oldukça dardır.
Adım adım gaz altı alüminyum kaynağının yapılışı,
1.Adım Uygun konfigürasyonu oluşturmak,
Pulse’lı yada double pulse’lı bir kaynak makinesini seçtikten sonra uygun kaynak teli seçmemiz gerekmektedir. Her bir alüminyum serisini her alüminyum kaynak teli ile kaynatamayız. Yukarıda alüminyum serilerinde uygun tel seçimlerini belirtmiştik. Telimizin normunu belirledikten sonra çapını belirlememiz gerekmektedir. Alüminyum kaynak teli oldukça yumuşak bir tel olduğu için, tel sürme esnasında bir çok problem ihtimali oluşur. Kaynak teli ayarladığımız hızlarda gelmezse ark yüksek voltaj etkisi gibi davranarak kontak tip memeye doğru yukarı çıkar ve sonunda kontak tip memeye yapışır. Tel kontak tip memeye yapışınca, makara grubundan sarmaya başlar. Prosesi oldukça yavaşlattığı gibi maliyetleri de yukarı çıkartır. Bu yüzden 0.8mm’den mümkün oldukça kaçınılmalıdır. Kaynak torcu bu olumsuz nedenlerden ötürü 3 metrenin üstünde olmaması gerekir. Torcun tel sürme spirali çelik değil teflon spiral olmalıdır. Tel sürme makaraları ve kontak tip alüminyuma uygun olan seri olmak zorundadır. Kullanacağımız kaynak gazı saf argon olmalıdır. Argon yerine helyum yada helyum argon karışımları da kullanılır. Helyum maliyeti oldukça yukarı çıkartırken kaynakta nufuziyeti artırır.
2.Adım Ön temizlik,
Kaynağa başlamadan önce ön temizlik yapmak önemlidir. Alüminyum oksit tabasını her ne kadar da pulse yöntemi ile yırtabilsek de, daha güzel görseller için alüminyuma uygun olan ekipmanlar kullanarak temizlenmesinde fayda var.
3.Adım Parametre ayarlamak,
Alüminyum kaynağında parametreler farklı sonuçlar doğurabilir. Çelik kaynağı gibi reaksiyon alamayız. Amper voltaj pulse veya double pulse ayarlarını malzememizin kalınlığına ve pozisyona göre deneyerek ayarlamalıyız. Bir çok yerde kaynak kalınlığına göre parametre aralıkları göreceksiniz. Bu çok doğru bir önerge değildir. Kaynakta bir çok farklı majör değişken vardır. Bunların hepsini bir araya getirip bir parametre oluşturmak mümkün değildir.
Isı iletkenliğine göre sıralanan genel metaller
Sıra Metal Isı İletkenliği [BTU / (saat · ft⋅ ° F)]
1 Bakır 223
2 Alüminyum 118
3 Pirinç 64
4 Çelik 17
5 Bronz 15
Alüminyum ısı iletkenliği oldukça yüksek olduğundan ark başlangıcında kaynak makinesinde sıcak başlangıç seçeneğini aktif edebiliriz. Bu sayede kaynağın başı da ortaları gibi homojen olacaktır.
4.Adım Kaynak esnasında dikkat etmemiz gerekenler,
Kaynak torcu her zaman aşağıda ki resimde belirtildiği gibi gazı öne almalıdır. Aksi taktirde kaynak görseli kötü olacaktır.
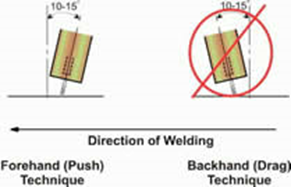
Çelik kaynağının aksine alüminyum gaz altı kaynağında, kaynak gazını oldukça yüksek debilerde tutmamız gerekir. Mümkün oldukça gaz saatinde son değerlere yaklaştırmak bile iyi olacaktır. Kaynak bittiği noktada torcu hemen kaldırmamız gerekir. Son gaz en az dört beş saniye daha akıp krater çatlağı riskini ve görsel kirlenmeyi önleyecektir.